Rethinking belt guide systems for curved belt conveyors.
Success stories are written when ideas turn into solutions – and this is precisely the story behind faigle’s latest breakthrough. For its customer motion06, faigle developed an innovative belt guide system that not only significantly reduces assembly times thanks to tool-free fitting, but also revolutionises the entire assembly experience. Featuring fewer components and a sophisticated design, faigle’s solution delivers a combination of efficiency and user friendliness.
motion06 sets the standards worldwide when it comes to high-performance curved conveyors – at logistics centres, e-commerce facilities and airports alike. Plastics specialist faigle has been working closely with motion06 since 2011. And their partnership has gone from strength to strength thanks to innovative plastics solutions.
So when motion06 asked whether faigle – which specialises in alternatives to metal parts – would be able to produce a plastic T-head bolt, it triggered a wide-ranging search for a potential solution. Instead of simply substituting a metal bolt for a plastic alternative with a bayonet fitting – which would only have delivered minimal added value anyway – faigle decided to think bigger, developing a ground-breaking component solution that goes way beyond the actual bolt.
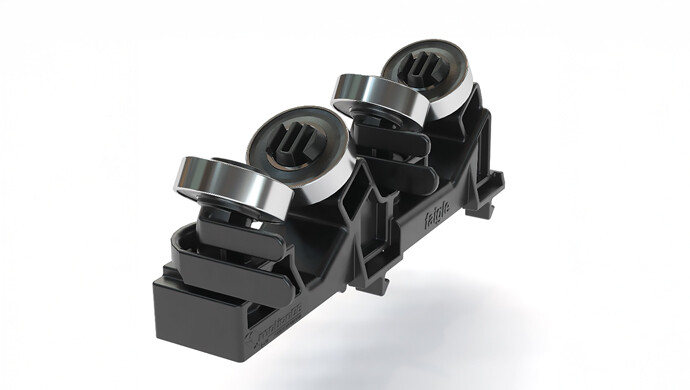
Challenges facing curved belt conveyors
Also referred to as CBCs, curved belt conveyors play a central role in conveying systems and can be found at airports and parcel distribution centres all over the world. At these facilities, belt guide systems – which are integrated into the curved aluminium profile – ensure that the edge of the conveyor belt is securely stretched outwards at the outer side of the belt. This precise guidance plays a decisive part in ensuring reliable operation, and also enhances the effi- ciency and durability of conveyor systems.
The previous design called for complex and time-consuming assembly using T-head bolts. By contrast, faigle’s new solution opens the door to significantly more straightforward and faster assembly, which translates into considerable optimisation of the entire process.
20 minutes saved! faigle’s new belt guide system.
Developed in close cooperation with motion06, the new design for the belt guide system completely removes the need for bolts and additional fasteners. The smart, joined-up design allows for tool-free assembly, while also raising the bar in terms of efficiency and handling.
The entire belt guide system is produced using cost-effective injection moulding processes at faigle’s plant in Hard, in the Austrian province of Vorarlberg. It comprises a single, pre-assembled unit that includes all of the necessary components: a holder, two rotating holders, a twist lock, compression spring, an adhesive tape, as well as four type 6004 2RS ball bearings. These ball bearings were selected because they can also function without any problems in freezer environments, where temperatures can be as low as -30°C. An integrated lever mechanism means that the ball bearings can simply be pivoted to the side, allowing the edge of the conveyor belt to be easily attached to or detached from the holder.
The result: a significant reduction in assembly times – on average 20 minutes per curve – depending on the curve geometry.
“Close cooperation and our long-standing partnership gave rise to the redesign of an existing product, which saves time for both the assembly team and the maintenance team, as well as minimising storage costs,” explains Florian Diemling, Head of R&D at motion06.
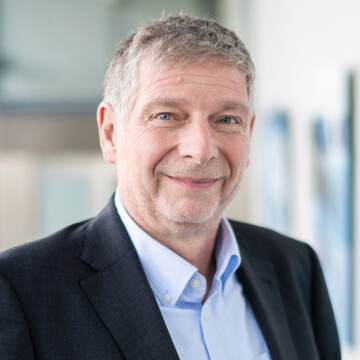
Christian Skopec
GLOBAL KEY ACCOUNT MANAGER AT FAIGLE
Meticulously tested, perfectly adapted
motion06 carried out intensive testing using a range of test curves and true-to-life assembly trials with the aim of ensuring that the required levels of reliability and durability were achieved. These tests underlined the component’s trouble-free assembly and functionality, while also opening up the possibility of making targeted adjustments. This resulted in components that can be installed without any difficulties and are extremely durable – meaning that they meet all of the demands placed on high-performance solutions for conveying systems.

Conclusion
Download Case Study

<iframe width="1500px" height="1190px" src="https://www.yumpu.com/en/embed/view/QmxVL0MPGUKT9ik1" frameborder="0" allowfullscreen="true" allowtransparency="true"></iframe>
<style>.embed-container { position: relative; padding-bottom:56.25%; height:0; overflow: hidden; max-width: 100%!important; } .embed-container iframe, .embed-container object, .embed-container embed { position: absolute; top: 0; left: 0; width: 100%; height: 100%;}</style><div class='embed-container' data-page-width='452' data-page-height='640' id='ypembedcontainer' ><iframe src="https://www.yumpu.com/en/embed/view/QmxVL0MPGUKT9ik1" frameborder="0" allowfullscreen="true" allowtransparency="true"></iframe></div><script src='https://players.yumpu.com/modules/embed/yp_r_iframe.js' ></script>
How can I help you?
Hi, I’m Christian Skopec. I’d be happy to talk to you about our products and answer any questions you might have on our custom solutions.
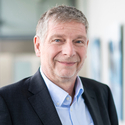