Case study: 2K wheel for Kardex
Thanks to a combination of innovative spirit and close collaboration, Kardex and the faigle Group have jointly developed a new guiding wheel for the Vertical Lift Module (VLM) storage system. Made from high-performance plastics, the new wheel’s lightweight construction gives it a clear edge over its predecessor. And this small part can also effortlessly withstand the huge forces it is exposed to at high operating speeds. Another advantage of this faigle innovation: production using injection moulding delivers clear benefits when it comes to cost effectiveness.
Substantial loads and relatively high speeds in combination with a comparatively small diameter – wheels used in storage systems must be able to handle significant forces. These challenging conditions lead to major technological complexities that previously called for the use of cast polyurethane (PU) wheels with a heavy metal hub.
faigle decided to take on this challenge and has developed a guiding wheel that can not only withstand these forces, but can also be produced as an all-plastic solution using high-efficiency injection moulding processes.
The innovative new component has been deployed in Kardex’s Vertical Lift Module (VLM), a storage system for small parts, where items are stored on various levels in a vertical tower. The items are removed from or placed in the system by means of a lift that moves between the different levels. In collaboration with Kardex, Austrian plastics specialist faigle designed a guiding wheel that is geared precisely to this sophisticated application and delivers a host of benefits.
Analysis and experience combine to create the ideal product
Delivering a suitable product called for in-depth analysis of the installation set-up. Thanks to its 50-plus years of experience in designing wheels for intralogistics systems, faigle was able to develop the ideal solution: a guiding wheel featuring a heavy-duty tire made from PAS-PU H – a thermoplastic elastomer – as well as a slimline, fibre-glass-reinforced polyamide hub, an overmoulded ball bearing and a custom wheel design. This ingenious solution was the key to meeting the development objective: “PAS-PU H and fibre-glass-reinforced polyamide can handle heavy loads despite the small diameter of the wheel,” explains Clemens Vögel, Global Key Account Manager at faigle. “Injection moulding ensures excellent bonding between the plastic components. Which is especially important here, because our aim was to develop guiding wheels that can operate completely reliably and remain maintenance-free for years on end,” he adds.
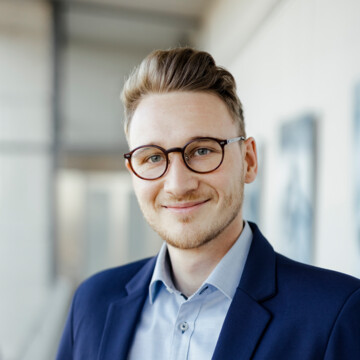
Clemens Vögel
GLOBAL KEY ACCOUNT MANAGER BEI FAIGLE
Good damping properties, low weight
The new component’s reliability is hugely impressive: precise concentricity coupled with a soft tire give the wheel its outstanding damping properties. And this lays the foundations for secure goods handling and low-vibration operations. Another factor that sets the new guiding wheel apart: the reduced weight compared to the cast wheels with heavy metal hubs that were used previously. This is vital because the lighter the components, the less energy is required for acceleration and motion.
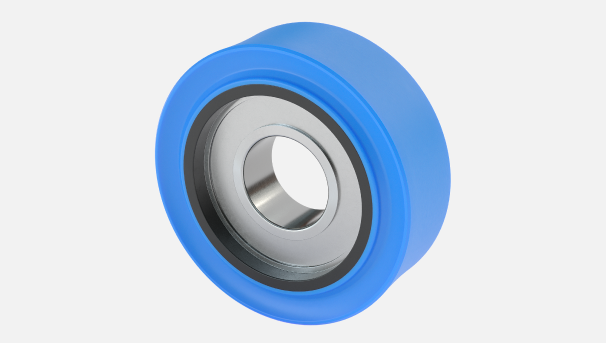
Efficient production and short lead times
What’s more, high-efficiency injection moulding not only delivers advantages in terms of cost and quality – it also translates into unbeatable lead times. Shorter production cycles enable faigle to guarantee faster availability even in the event of short-term demand peaks. faigle’s production facilities in Europe and China – in Hard, Vorarlberg, and Suzhou respectively – open up additional flexibility, enabling the company to deliver products precisely where they are needed in next to no time.
Dennis Halbherr
RESPONSIBLE FOR PROCUREMENT SUPPLY CHAIN AT KARDEX REMSTAR
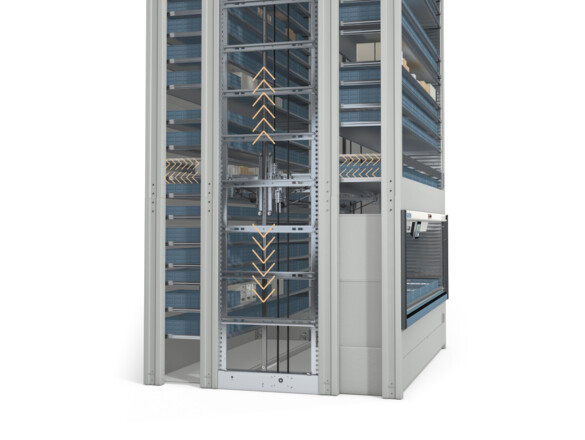
Comprehensive testing ensures outstanding quality
Kardex’s Vertical Lift Module (VLM) is an en- closed, shelf-based storage system that offers increased capacity while also taking up less floor space.
Regardless of where faigle produces the wheels, they always undergo rigorous testing. During the development phase, the plastics specialist uses cutting-edge test benches that allow for detailed analysis and also support quality assurance processes for volume production. faigle’s experts put the new wheel through its paces, evaluating its concentricity, hydrolysis resistance and flattening in the most minute detail. Short-term and endurance testing delivered valuable insights into the new wheel’s capabilities, with a view to ensuring its reliability, durability and fitness for purpose in the application. The evaluation continued at Kardex’s in-house testing facility. “Reliable products are paramount for our customers. So the focus is on supplying high quality, right down to the very last detail. faigle helped us to achieve this – and to further fine-tune our VLM,” emphasises Dennis Halbherr, who is responsible for the procurement supply chain at Kardex Remstar.
How can I help you?
Hi, I’m Clemens Vögel. I’d be happy to talk to you about our products and answer any questions you might have on our custom solutions.
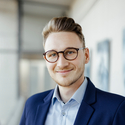