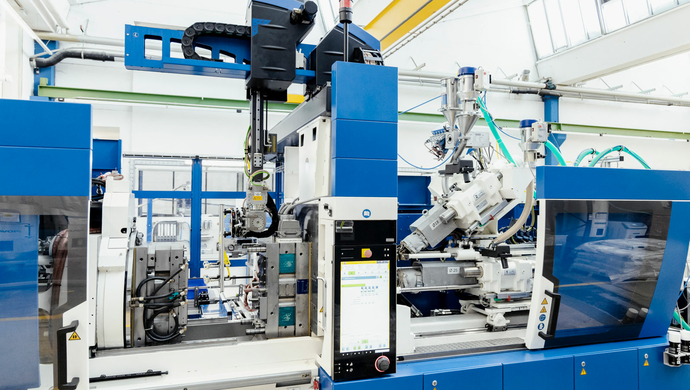
faigle’s high-performance plastic parts are the key to continuous, trouble-free production operations. Switching to faigle plastic components also allows plant operators to reduce heating and drive-energy consumption, which not only translates into significant cost savings but has a positive impact on the carbon footprint, too. Aligned precisely with customer requirements, the high-quality parts are a long-term alternative to metal or standard plastic parts thanks to their durability. The technology leader’s expertise stands out in the dimensional stability, low weight and the absence of lubricants for their products during operation.
Growing demand for plastic parts “Our highly dependable parts play an essential role in our customers’ supply chains. Interruption-free production processes are vital for our partners – standstills would be disastrous,” says Wolfgang Faigle. As Andrew Lanham, EVP, Customer & Product Strategies at YTY Group confirms: “We need partners who are totally reliable for our glove production. And faigle also uses its extensive plastics expertise to support us in the development of innovative, custom solutions for our production operations.”
Tailor-made for complex production processes faigle always has an important part to play when it comes to safety. “Optimum quality and high load capacity are vital in safety-critical parts. With complex production procedures like those for gloves, our plastic parts ensure that the products meet the desired quality standards and are free of flaws such as tears and impurities – even when working with sensitive materials with a thickness of just 0.1mm,” explains faigle’s Vice President Marketing & Sales, Holger Schröder.
WOLFGANG FAIGLE
CEO & OWNER, FAIGLE GROUP